Support small batches and multiple varieties
Facing the complex and ever-changing market demand (small batches and multiple varieties), we support business development through technical means.APSThere are not only relatively simple algorithms, such as the shortest due date algorithm, the shortest working procedure algorithm, but also complex algorithms, such as neural network, simulated annealing, genetic algorithm, tabu search method, etc.
Provide direction for production improvement
It can correctly predict the manufacturing status and possible problems in the near future. Simulated scheduling can be performed,what-ifAnalysis, that is, if what kind of countermeasures are used, what kind of results can be obtained.
Cost reduction
By optimizing the production sequence and batch size, the time for changing lines and preparation time in the production process are reduced, and energy consumption and material waste are reduced.
Through intelligent scheduling of the maintenance plan of production equipment,APSHelps prevent equipment failure, reduce downtime, and prolong equipment life.
Optimize resource utilization, deduce material procurement requirements, and respond to changing market requirements
Increasing production capacity
Eliminate bottlenecks
Reducing Inventory Costs
Meet delivery schedule
Optimize the use of equipment
Improving profitability
Other Customers We Helped
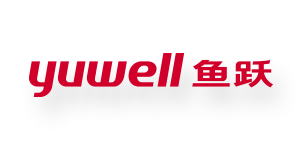
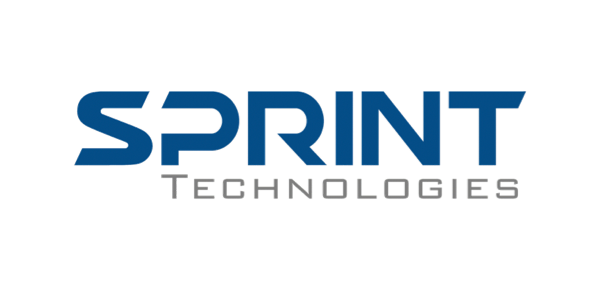
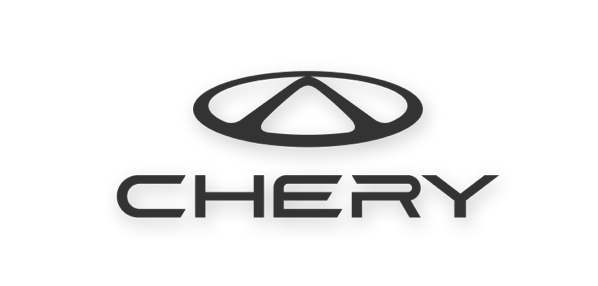
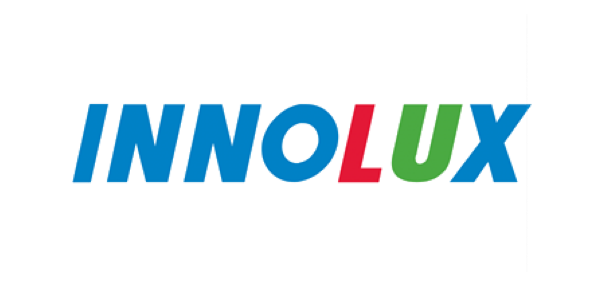
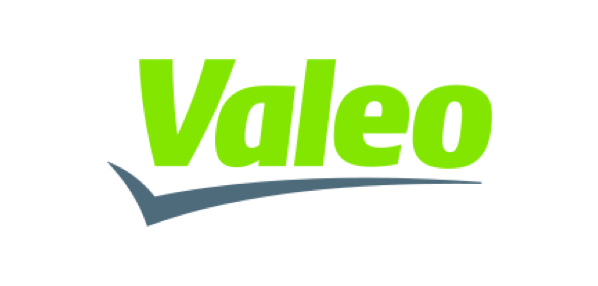