Accelerate product launch and delivery
MightyBOMAndCADSupport capability, graphical process designer, robust work instruction book writing, revision control and approval, accelerate the introduction of new products in a perfect and timely manner.
Maintaining profitability
Process implementation, lean material management, and complete connectivity are just a few of the capabilities that ensure you deliver the highest quality at the lowest possible cost.
Make your customers happy
With fast product launches, the perfectECOPerfect product quality, and timely response to customer analysis and tracking requests to meet customer satisfaction.
The electronic and electrical industry introduces electronic assembly when solving problems such as high manufacturing costs, unstable product quality, difficult monitoring of production processes, low production delivery efficiency, and difficult process traceability.MESSystem is a comprehensive and effective solution. Through the optimization of material management, quality management, production process monitoring and order management, the electronic and electrical industry can meet the challenges of market changes and informatization while improving efficiency, reducing costs and improving quality stability.
Reduced production cycle30%
Process traceability
We've also helped a few other clients
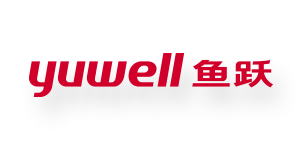
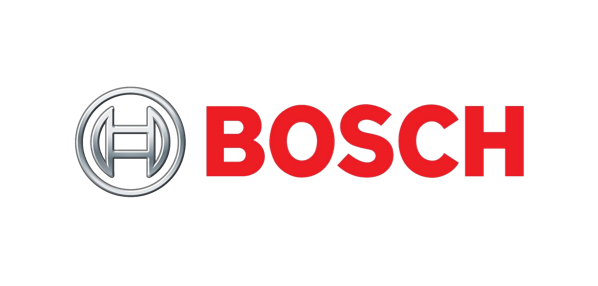
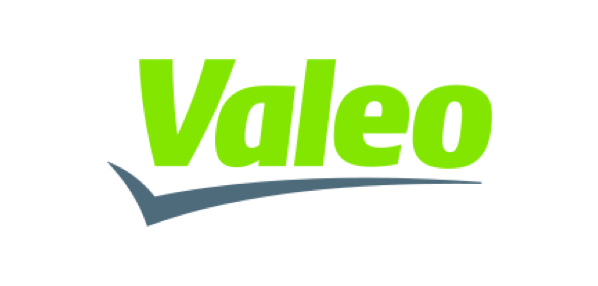
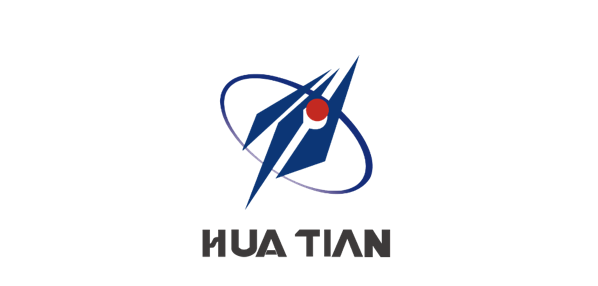
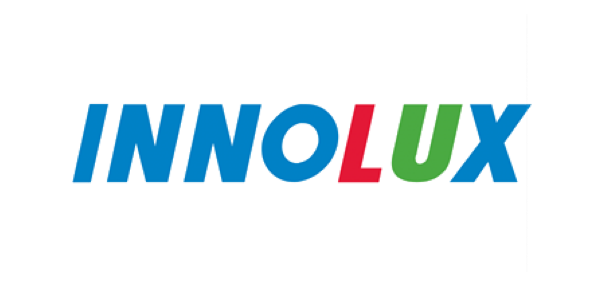